深入探讨高效无卤阻燃剂对材料性能与安全性的提升作用
在全球对消防安全与环境保护日益重视的背景下,高效无卤阻燃剂凭借环保、阻燃性能优异等特点,成为材料领域的研究热点与应用关键。传统含卤阻燃剂虽阻燃效果突出,但燃烧时释放的有毒有害气体严重威胁生命安全与生态环境,促使高效无卤阻燃剂快速发展。本文将从多个维度深入探讨高效无卤阻燃剂,解析其对材料性能与安全性的提升机制及应用效果。
一、高效无卤阻燃剂的核心分类与作用原理
1.1 分类详述
高效无卤阻燃剂依据化学结构与作用特性,主要分为磷系、氮系、硅系、金属氢氧化物系以及磷 - 氮协同体系等类别 。磷系阻燃剂包含磷酸酯类、红磷等,通过受热分解形成焦磷酸盐等稳定物质,在材料表面构建炭层,实现隔热隔氧;氮系阻燃剂如三聚氰胺及其衍生物,受热分解产生氮气、氨气等惰性气体,稀释氧气浓度与可燃气体浓度,中断燃烧反应;硅系阻燃剂凭借硅氧键的独特稳定性,在材料表面生成硅氧炭层,提升材料的阻燃与热稳定性能;金属氢氧化物系中的氢氧化铝、氢氧化镁,受热分解吸收热量,释放结晶水稀释氧气,分解产物还能增强炭层强度;磷 - 氮协同体系则通过磷系与氮系阻燃剂的协同效应,发挥气相阻燃、凝聚相阻燃等多重作用,显著提升阻燃效率 。
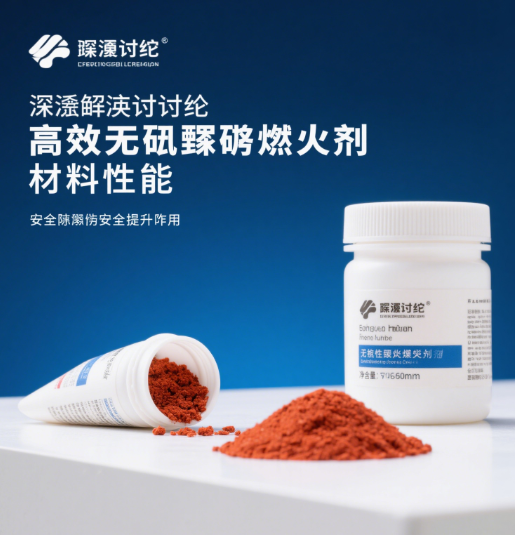
1.2 作用原理深度剖析
- 气相阻燃机制:部分高效无卤阻燃剂在高温下分解产生大量不燃性气体,如氮系阻燃剂分解生成的氮气、氨气,硅系阻燃剂分解产生的硅氧烷气体。这些气体充斥在燃烧区域,降低氧气浓度与可燃气体浓度,稀释燃烧反应所需的助燃剂与燃料,从而抑制燃烧反应的持续进行 。
- 凝聚相阻燃机制:磷系、硅系等阻燃剂受热后,会在材料表面发生一系列化学反应,形成致密、稳定的炭层或硅氧炭层。该炭层如同隔热隔氧的屏障,阻止热量向材料内部传递,隔绝氧气与可燃材料接触,同时还能抑制可燃气体的逸出,切断燃烧的链式反应 。
- 中断自由基反应机制:燃烧过程本质是自由基链式反应,高效无卤阻燃剂能够捕捉燃烧过程中产生的自由基,如羟基自由基、氢自由基等。以磷系阻燃剂为例,其分解产物可与自由基反应,生成稳定的化合物,中断自由基的传递,从而有效抑制燃烧的蔓延 。
二、高效无卤阻燃剂的关键产品参数与性能优势
2.1 关键产品参数
高效无卤阻燃剂的产品参数直接决定其阻燃效果与在材料中的应用适配性。核心参数包括极限氧指数(LOI)、热分解温度、添加量、与基体材料的相容性、阻燃效率等 。极限氧指数是衡量材料难燃程度的重要指标,LOI 值越高,材料在空气中维持燃烧所需的氧气浓度越高,阻燃性能越佳;热分解温度反映阻燃剂的热稳定性能,较高的热分解温度确保阻燃剂在材料加工过程中不提前分解失效;添加量关乎阻燃效果与成本控制,适量添加既能实现理想阻燃效果,又可降低成本;与基体材料的相容性影响阻燃剂在材料中的分散均匀性,良好的相容性有助于充分发挥阻燃性能 。表 1 展示了几种常见高效无卤阻燃剂的关键产品参数:
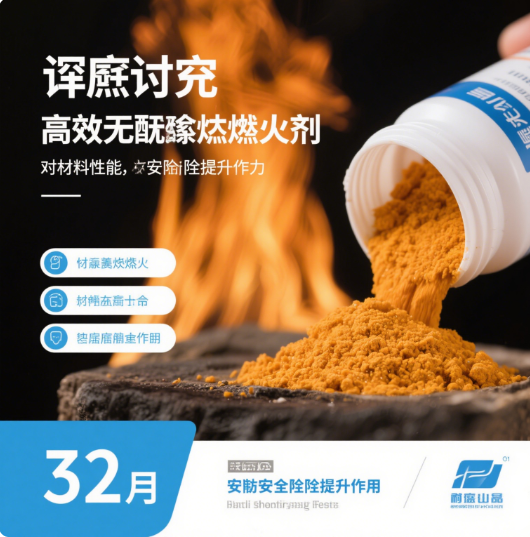
2.2 性能优势
相较于传统含卤阻燃剂,高效无卤阻燃剂在环保性、阻燃性能持久性、综合性能等方面展现出显著优势 。在环保层面,燃烧过程中不产生卤化氢、二噁英等有毒有害气体,降低火灾中的二次危害,减少对环境与人体健康的威胁;从阻燃性能持久性来看,与基体材料通过化学键或物理缠绕等方式紧密结合,不易迁移、析出,能够长期稳定地保持材料的阻燃性能;在综合性能方面,通过合理配方设计与工艺优化,在提升阻燃性能的同时,对材料的力学性能、加工性能、电气性能等影响较小,甚至可赋予材料新的性能 。
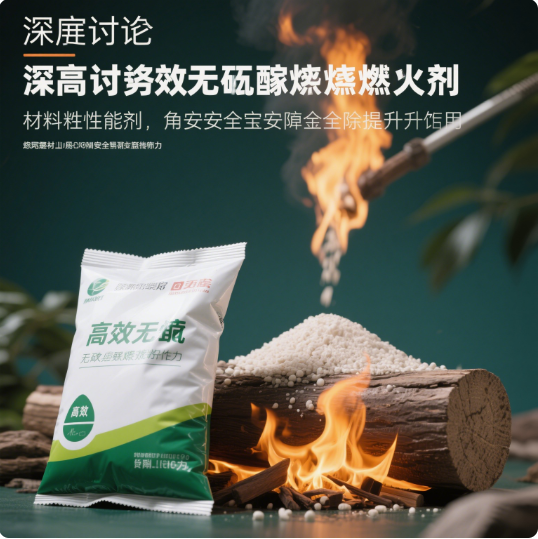
三、高效无卤阻燃剂在多领域材料中的应用实践
3.1 建筑领域材料应用
在建筑领域,塑料建材、纤维织物、涂料等材料广泛使用高效无卤阻燃剂提升安全性 。以塑料建材中的聚氯乙烯(PVC)门窗为例,采用磷 - 氮协同体系的膨胀型阻燃剂进行改性,添加 22% 的阻燃剂后,PVC 门窗的极限氧指数从 23% 提升至 36%,垂直燃烧等级达到 UL - 94 V - 0 级,且燃烧时烟雾释放量大幅降低 。在纤维织物方面,针对建筑装饰用的聚酯窗帘,使用磷酸酯类磷系阻燃剂进行处理,添加 15% 的阻燃剂后,窗帘的垂直燃烧等级达到 GB/T 5455 - 2014 B1 级,有效阻止火焰蔓延 。在涂料应用中,于水性丙烯酸外墙涂料中加入硅 - 磷协同阻燃剂,当添加量为 20% 时,涂料的极限氧指数达到 32%,涂层的附着力、耐候性等性能良好,显著提升建筑外墙的阻燃安全性 。
3.2 电子电器领域材料应用
电子电器产品对材料的阻燃性能与电气性能要求极高,高效无卤阻燃剂在此领域发挥关键作用 。在聚碳酸酯(PC)制成的电子电器外壳中,添加 18% 的氮系阻燃剂三聚氰胺聚磷酸盐,PC 外壳的极限氧指数提升至 34%,满足 UL - 94 V - 0 级阻燃标准,同时材料的电气绝缘性能基本不受影响 。对于印刷电路板(PCB)常用的环氧树脂,采用含磷环氧树脂阻燃剂进行改性,添加 12% 的阻燃剂后,环氧树脂的热稳定性显著提高,热分解温度提升约 50℃,阻燃性能达到 UL - 94 V - 0 级,保障电子电器产品在使用过程中的消防安全 。
3.3 汽车内饰领域材料应用
汽车内饰材料不仅要求阻燃性能,还需满足低烟、低毒、耐候等性能要求,高效无卤阻燃剂成为理想选择 。在聚丙烯(PP)制成的汽车座椅面料中,添加 15% 的金属氢氧化物系氢氧化镁阻燃剂,面料的极限氧指数提升至 28%,垂直燃烧性能达到 FMVSS 302 标准要求,且燃烧时烟雾少、无毒气释放 。对于汽车内饰的聚氨酯泡沫材料,使用硅系阻燃剂进行改性,添加 10% 的阻燃剂后,泡沫材料的热释放速率降低 45%,有效延缓火灾蔓延,同时保持良好的柔软性与回弹性 。
四、影响高效无卤阻燃剂应用效果的关键因素
4.1 阻燃剂自身特性的影响
阻燃剂的化学结构、热稳定性、阻燃效率等自身特性对应用效果起决定性作用 。化学结构决定其阻燃机制与反应活性,例如含芳香环结构的磷系阻燃剂,形成的炭层稳定性更高;热稳定性差的阻燃剂在高温加工过程中易分解失效,导致阻燃性能下降;阻燃效率低的阻燃剂则需增加添加量,可能影响材料的其他性能 。
4.2 基体材料性质的影响
不同基体材料的化学结构、物理性能、极性等差异,对阻燃剂的相容性与分散性要求不同 。极性基体材料如环氧树脂、聚氨酯,与极性阻燃剂相容性较好;非极性基体材料如聚烯烃,需选择非极性或经过表面改性的阻燃剂,以确保阻燃剂均匀分散,充分发挥阻燃作用 。
4.3 加工工艺条件的影响
加工温度、时间、压力等工艺条件显著影响阻燃剂的应用效果 。过高的加工温度可能使阻燃剂分解或与基体材料发生不良反应;加工时间不足会导致阻燃剂与基体材料反应不充分;压力不合适则影响材料的密实度与阻燃剂的分散均匀性 。例如,在挤出成型工艺中,聚烯烃材料与阻燃剂共混时,需精确控制温度在 180 - 200℃,加工时间 3 - 5 分钟,以获得阻燃效果与材料性能 。
五、高效无卤阻燃剂的研究前沿与发展趋势
5.1 新型结构与协同体系开发
当前,研究人员致力于开发新型结构的高效无卤阻燃剂,如纳米阻燃剂、超支化阻燃剂、树枝状阻燃剂等 。纳米阻燃剂凭借纳米级尺寸效应,少量添加即可显著提升材料阻燃性能;超支化与树枝状阻燃剂具有独特的分子结构,可实现多功能集成 。同时,探索不同阻燃剂之间的协同体系,如磷 - 氮 - 硅协同体系,通过多种阻燃机制协同作用,进一步提高阻燃效率 。
5.2 多功能一体化发展
高效无卤阻燃剂正朝着多功能一体化方向发展,除阻燃性能外,还赋予材料抗菌、自清洁、隔热保温、电磁屏蔽等功能 。通过将阻燃剂与其他功能性添加剂复合或对阻燃剂进行功能化改性,开发出满足多领域需求的高性能材料 。例如,将具有抗菌功能的金属离子引入阻燃剂结构中,制备出兼具阻燃与抗菌性能的复合材料 。
5.3 绿色可持续发展
在环保要求日益严苛的趋势下,绿色可持续发展成为高效无卤阻燃剂的重要方向 。开发可生物降解的阻燃剂,使用可再生资源作为原料,降低阻燃剂生产过程中的能耗与污染,提高阻燃剂的回收利用率等成为研究重点 。如以天然植物提取物为原料制备阻燃剂,既实现环保目标,又拓宽了阻燃剂的原料来源 。
六、结论
高效无卤阻燃剂凭借独特的阻燃机制、优异的产品性能与广泛的应用领域,在提升材料性能与安全性方面发挥着不可替代的作用。通过深入了解其分类、作用原理、产品参数及应用影响因素,结合各领域材料需求合理选择与使用,能够有效增强材料的阻燃性能,降低火灾风险 。随着研究的不断深入与技术创新,高效无卤阻燃剂将在建筑、电子电器、汽车等众多领域持续发展,为推动材料行业向绿色、安全、高性能方向迈进提供强大动力 。
参考文献
[1] 张明,刘华。无卤阻燃剂的研究进展与应用 [J]. 高分子材料科学与工程,2023, 39 (5): 1 - 8.
[2] Smith J, Johnson A. Recent Advances in Halogen - Free Flame Retardants for Polymer Materials [J]. Progress in Polymer Science, 2022, 128: 101485.
[3] 王强,陈丽。磷 - 氮协同阻燃体系在塑料中的应用研究 [J]. 塑料工业,2021, 49 (7): 1 - 5.
[4] Brown C, Green D. Application of Silicone - Based Flame Retardants in Electronic Materials [J]. Journal of Electronic Materials, 2020, 49 (10): 6537 - 6545.
[5] 赵刚,孙明。金属氢氧化物阻燃剂在汽车内饰材料中的应用 [J]. 汽车工艺与材料,2019, (8): 32 - 36.